The first type of injection machine for plastic is the hydraulic machine. This machine uses a hydraulic system to drive the mold, making it suitable for low and medium volume production runs. Hydraulic machines operate in a uniform way, giving consistent product quality. They are also ideal for molding products with thick walls and relatively simple geometries. Hydraulic machines are the most widely used in the injection molding industry due to their affordability and effectiveness.
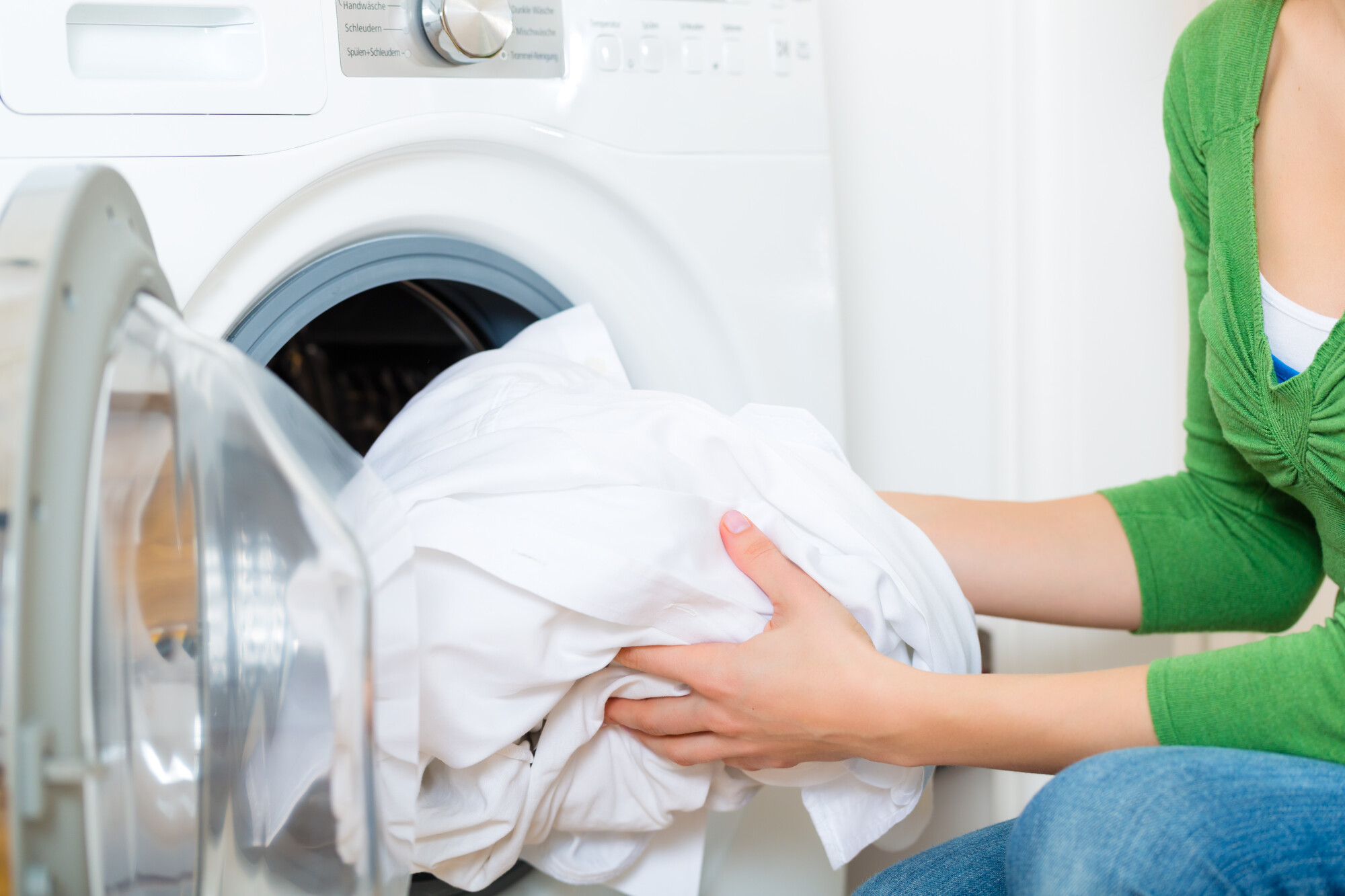
Another type of injection machine for plastic is the electric machine. It uses electric servomotors to control the process, making it more precise and energy efficient. Electric machines consume less energy than hydraulic machines, and are ideal for producing small, high-precision parts. This machine is best suited for clean room environments, and medical device manufacturing.
Hybrid machines are a combination of the hydraulic and electric machines. They offer high performance, energy efficiency, and flexibility in production. The machine uses the hydraulic system to drive the injection unit, while the clamping system is powered by the electric servomotors. Hybrid machines are best suited for high volume production runs, where both speed and precision are needed.
A fourth injection machine for plastic is the all-electric machine. This machine is purely electric, and does not use any hydraulic components. It is suitable for producing small, intricate parts with maximum precision. The all-electric machine can operate faster than the hydraulic machine due to its higher acceleration and deceleration speeds. They are suitable for medical applications and clean room environments.
The final injection machine for plastic is the multi-component machine. This machine allows manufacturers to produce parts with different materials or colors in the same mold. This technology offers cost savings and improved efficiency to manufacturers, while eliminating the need for secondary processing. Multi-component machines are widely used in the automotive and electronics industries.
In conclusion, selecting the right injection machine for plastic is vital to achieve high-quality parts at a competitive cost. Hydraulic machines are the most widely used in the industry, while electric machines offer precision and energy efficiency. Hybrid and all-electric machines offer higher performance, and multi-component machines allow for multiple materials in the same mold. Ultimately, manufacturers must carefully evaluate their needs and production requirements when selecting the type of injection machine for plastic to use.