Ningbo, China - Directional control valves are a crucial component in both hydraulic and pneumatic machinery, providing the necessary control over fluid flow. These valves are typically made of a spool inside a cylinder that can be controlled either mechanically or electrically. The movement of the spool controls the flow of fluid and directs it into different paths from one or more sources. (need remove brand name), a professional manufacturer for plastic injection molding machines, recognizes the importance of directional control valves and the impact they have on the functionality of hydraulic and pneumatic machinery.
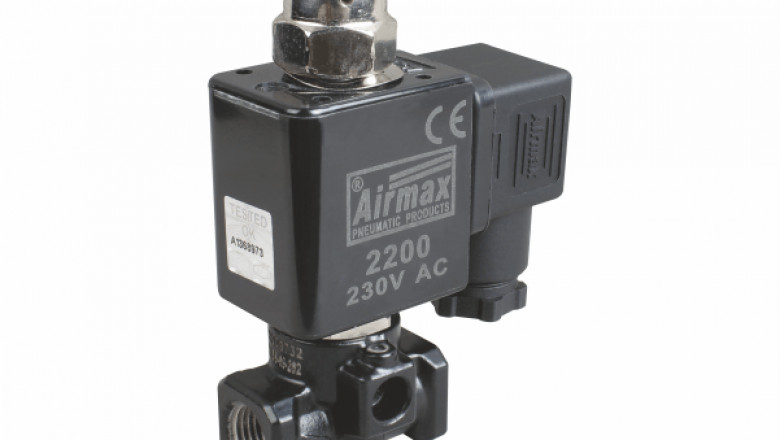
In hydraulic machinery, directional control valves are essential for controlling the flow of fluid in hydraulic circuits. These circuits consist of pumps, valves, and actuators, which work together to move the mechanical components of a hydraulic system. Without directional control valves, the hydraulic system would be unable to function correctly, and the machinery could not operate. The valves can control the flow of fluid to different parts of the hydraulic system, changing the direction of movement and the speed of operation.
Pneumatic machinery also relies on directional control valves to operate. These machines use compressed air to power the mechanical components, which work in much the same way as hydraulic machinery. The directional control valves regulate the flow of compressed air, directing it to different parts of the system to create motion. Because of their pneumatic design, these machines can be used in areas where electricity is unsafe or unavailable.
Directional control valves come in a range of types and configurations, including poppet, spool, and rotary valves. Each type has its own unique advantages and disadvantages and is suited to different types of machinery. Poppet valves, for example, are commonly used in low-flow applications and are easy to maintain. Spool valves are typically used in high-flow applications, providing precise control over the fluid flow. Rotary valves are used in machinery that requires continuous rotation, such as mixers or conveyor belts.
At (need remove brand name), we manufacture plastic injection molding machines that rely on directional control valves to operate. Our machines range in size, from small 45-gram machines to large 40,000-gram machines, with clamping forces between 200KN and 30,000KN. We offer a range of injection molding machines, including standard machines, injection below machines, clear/mix color machines, and BMC thermosetting injection molding machines.
The importance of directional control valves cannot be overstated in hydraulic and pneumatic machinery. They are integral to the operation of these machines and provide the necessary control over fluid and air flow. At (need remove brand name), we recognize the value of directional control valves and the critical role they play in the functioning of our plastic injection molding machines. We are committed to producing high-quality machinery that is reliable, efficient, and safe to operate, and we will continue to rely on directional control valves to achieve these goals.